Lifan 107 Owners Manual
Firstly, an engine service manual for the SDG 107 does not (and likely never will) exist. Perhaps this thread can serve as one - at least answering some of the more important questions. I got an SDG 107 engine, partially disassembled, when I bought a pile of fiddy parts. I was impressed with its robust construction, and felt it was worth putting some effort into. Tucker Motorcycle Supply, an online parts supplier, has exploded parts views of the engine. I had a hard time installing the clutch, and discovered there is a bit of a trick to it.
The exploded view of the clutch assembly can be found here: After installing the clutch basket (items #15 and #7) on the shaft. The thick 'spline washer' (item #14) is next. Slide it on the shaft until it falls into the groove in the shaft. Then rotate the spline washer 1 spline. Next install the thinner 'washer' (item #16) with the tangs facing the spline washer. The tangs will lock the spline washer in the proper place to maintain clearance for the clutch basket when 'Spanner Nut M14x22mm' (item # 18) is eventually tightened. I also learned from talking with Jeff and Chris at SDG that you can tell a 2004 motor from a 2005 motor by the color of the cases.
The older motor was painted a shiny gray, whereas the newer motor has a natural aluminum finish. The 2005 motors also used an aluminum cylinder.
The 2004 model has a iron cylinder. Although heavier, the cast iron cylinder can be bored to build a 160cc motor.
Apparently, the 2004 motors have a bad reputation for catastrophic kickstart mechanism failure. However, I am told that if you 'don't kick it like an old Harley', the kickstart mechanism is reliable. If anyone has reliable information, I'd like to know the valve clearances and engine oil capacity. I have been working on mine, which is a 2004 model I got from Ebay, and about everything else.
SDG have parts, but don't really advertise that fact. I get the feeling that after they had to replace engine cases, etc, the whole thing got to be a loser for them and they dropped it. Pity, because I bought the thing on the fact that it is a 3 valve, a good idea as you can run more overlap and not have the valves hit, etc.
Mine, when new, had zero valve clearance, so I set the valves at about.003', which was a piece of notepaper thickness ( I have a feeler blade now!) The oil is standard capacity for one of these engines at 900 cc, 0.9L. About the bore, would love to put an aluminum cylinder on it and guess I will have to weld the extra bosses on it to accept the 3V's odd accessory bolt pattern on the head. I don't like the iron cylinder as you have to run a ton of bore clearance and the harder you work it the more clearnace you need. I also had some difficulty timing the cam. I don't think my cam-gear witness mark is in the correct location from the factory.
It appears to me about 1/2 tooth off. Anyone else had this problem? The TDC mark is definitely not exact. As you can see in this pic, I marked the correct location with a Sharpie. Also, I made a tool that marked exactly half-way between the cam cover mounting holes.
Then I used a machinist's square to identify.WHAT I ASSUME. is the correct location. At least with this method, there is not 1/2-tooth of error. If anyone has the cam timing specifications, I'd be willing to do the work to verify my assumption.
REMOVAL Prepare for Service 1. Position motorcycle on a suitable lift.
NOTE If vehicle is equipped with Harley-Davidson Smart Security System, see owner’s manual for instructions to disarm the system. To prevent accidental vehicle start-up, which could cause death or serious injury, disconnect negative (-) battery cable before proceeding. Disconnect battery cables, negative (-) battery cable first. Remove seat according to the instructions in the service manual. Refer to service manual to remove left saddlebag and side cover. When servicing the fuel system, do not smoke or allow open flame or sparks in the vicinity.
Gasoline is extremely flammable and highly explosive, which could result in death or serious injury. Remove fuel tank according to the instructions in the service manual. Remove Engine Components 1. Remove existing air cleaner assembly. Discard backplate but save remaining parts. Refer to AIR CLEANER REMOVAL in service manual. Remove existing exhaust system.
Refer to EXHAUST SYSTEM REMOVAL in service manual. Remove engine from chassis following the instructions in the service manual. Disassemble engine top end and bottom end. Refer to appropriate ENGINE sections in service manual. Remove existing clutch diaphragm spring. Refer to CLUTCH REMOVAL in service manual. The procedures in this instruction sheet should be performed by one experienced in precision measuring techniques.
Failure to meet tolerances called for in this instruction sheet can result in engine damage. (00511b) -J04793 1 2 is03517 1. O-ring counterbore 2.
Spigot bore Figure 1. Spigot Bore and O-Ring Counterbore Dimensions Table 1. Spigot Bore and O-Ring Counterbore Dimensions Depth Bore Description 1.625 +/- 0.010 in. (41.3 +/- 0.25 mm) 4.205 +/- 0.010 in. (107 +/- 0.25 mm) Spigot Bore 0.085 +/- 0.003 in.
(2.16 +/- 0.08 mm) 4.415 +/- 0.002 in. (112 +/- 0.05 mm) O-Ring Counter- bore is03456 Figure 2. Cylinder Wall MACHINE CRANKCASE Crankcase Boring Preparation NOTE During final assembly of the engine, Harley-Davidson recommends replacing the OE cylinder studs with Screamin’ Eagle High Tensile Studs (16505-01). Remove cylinder studs from the engine crankcase. Mask off all bearings and oil holes to prevent debris and contaminants from entering those areas. Inspect and clean engine case mating surfaces. See Figure 6.
Reassemble engine case with OE screws, except the top center screw between the cylinders, and tighten to specifications listed in service manual. NOTE To prevent damage to crankcase boring tool, it is important to replace the top center screw with a modified top center screw (1093). This screw is included in the Crankcase Boring Tool Kit (94419-06) and can be purchased separately from a Harley- Davidson dealer. Install modified top center screw (1093) between the cylinders and tighten to 50-90 in-lbs (5.6-10.2 Nm).
See Figure 1 and Table 1. Machine crankcase cylinder spigot bore and O-ring counterbore to the dimensions shown. Modify Crankcase Incoming search terms:. Cover the throttle bodies to prevent anything from dropping into the engine.
Remove the front seat and disconnect the battery. (Refer to Service Manual, Page 8-8) 2. Lift up the fuel tank. (Refer to Service Manual, Page 5-3) 3. Remove the air cleaner box. (Refer to Service Manual, Page 5-14) 4. Remove and replace the ISC valve.
(Refer to Service Manual, Page 5-25) NOTE: Since the ECM is also being replaced there is no need to perform the ISC valve preset operation. Install the air cleaner box in reverse order of removal. (Refer to Service Manual, Page 5-14) 6. Lower the fuel tank. (Refer to Service Manual, Page 5-3) 7. Remove the upper seat rail plate.
Disconnect and remove the ECM. (Figure 1) @ ISC Valve Mounting Screw Torque: 2.1± ±0.6 N.m (1.5± ±0.4 lb-ft)! Mazda wl turbo engine manual.
Carefully insert the ISC valve straight into the throttle body hole to prevent damaging the o-ring. Turn the ISC valve slightly to confirm that the o-ring has not twisted. Using the new screw provided in the replacement parts kit, make sure the screw is completely seated on the plate after the screw has been tightened to the specified torque. Remove and replace the ISC valve. (Refer to Service Manual, Page 5-25) NOTE: Since the ECM is also being replaced there is no need to perform the ISC valve preset operation.! Cover the throttle bodies to prevent anything from dropping into the engine.
Remove the front seat and disconnect the battery. (Refer to Service Manual, Page 8-8) 2. Lift up the fuel tank. (Refer to Service Manual, Page 5-3) 3.
Remove the air cleaner box. (Refer to Service Manual, Page 5-14) REPLACEMENT PROCEDURE: 8.
Install the new ECM in reverse order of removal. Apply thread lock to the upper plate mounting bolts when reinstalling the upper seat rail plate.
Incoming search terms:. During Break-In At 50 Miles (80 Kilometers): 1- Change engine oil and filter. 2- Inspect for fuel and oil leaks. 3- Inspect air cleaner element and service as required. 4- Check tightness of exterior fasteners, except head bolts. Engine Maintenance at 500 Miles (800 Kilometers): 1- Change engine oil and filter. 2- Inspect for fuel and oil leaks.
3- Inspect air cleaner element and service as required. 4- Check tightness of exterior fasteners, except head bolts. 5- Check operation of enrichment device and throttle controls. 6- Check engine idle speed. 7- Check tightness of engine mounts. Regular Service Intervals Regular lubrication and maintenance will help keep your new S&S engine operating at peak performance.
The following table presents the required service schedule for normal operating conditions. Failure to complete the required engine maintenance can result in engine damage and an increase in emissions. Please refer to the motorcycle owner’s manual for any additional required chassis maintenance. Engine Service Intervals Item Interval Engine Oil & Filter Change at 50, 500, 2,500 miles (80, 800, 4,000 kilometers), every 2,500 miles (4,000 kilometers) thereafter1 Air Cleaner Element Inspect at 50 and 500 miles (80 and 800 kilometers), every 2,500 miles (4,000 kilometers) thereafter2 Tappet Oil Screen Inspect every 2,500 miles (4,000 kilometers). Replace every 5,000 miles (8,000 kilometers). Petcock, Lines, & Fittings, Vacuum Lines Inspect at 50 and 500 miles (80 and 800 kilometers), every 2,500 miles (4,000 kilometers) thereafter. Fuel Tank Filter Screen & In-Line Fuel Filter (If used) Inspect every 5,000 miles (8,000 kilometers).
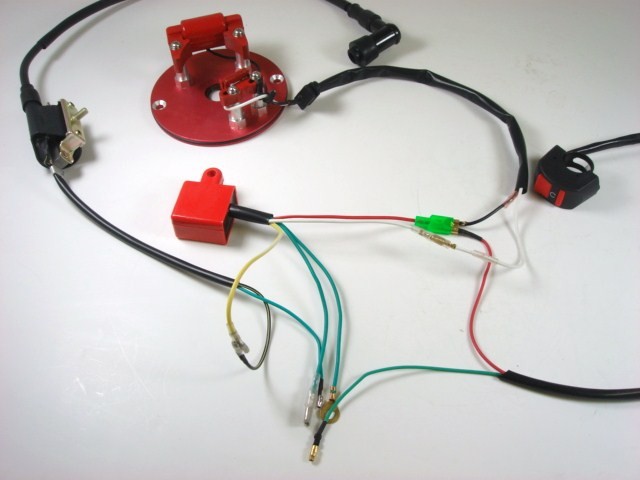
Engine Idle Speed Adjust as required. Operation of Throttle & Enrichment Device ControlsInspect at 500 miles (800 kilometers) and every 2,500 miles (4,000 kilometers) thereafter. Spark Plugs Inspect every 5,000 miles (8,000 kilometers). Replace every 10,000 miles (16,000 kilometers) or as needed. Ignition Timing Inspect every 5,000 miles (8,000 kilometers).
Engine Mounts Inspect at 500 miles (800 kilometers) and every 5,000 miles (8,000 kilometers) thereafter. External Fasteners Except Engine Head Bolts Re-torque at 500 miles (800 kilometers) and every 5,000 miles (8,000 kilometers) thereafter. 1- S&S recommends that petroleum-based oil not specifically formulated for motorcycles should be changed every 1,000 miles (1,600 kilometers) after the break-in period. 2- Replace more frequently if required or if engine is operated in a dusty environment.
Incoming search terms:. REMOVAL NOTE This Instruction Sheet covers several different Harley-Davidson models and years.
Be sure to locate and follow the procedures that apply to the motorcycle receiving the new guard. For Models without Lower Fairings 1. Proceed to For All Models section. For Model FLHTCUI (Ultra Classic Electra Glide) with Factory-Installed Lower Fairings 1.

Remove the lower fairings following the instructions in the appropriate Service Manual. When the lower fairings have been removed, proceed to For All Models section. For Models FLHR/I (Road King), FLHT (Electra Glide Standard) or FLHTC/I (Electra Glide Classic) with Harley-Davidson Genuine Motor Accessory Lower Fairings 1. See Figure 1. Remove the two black screws (1) that attach the fairing cap (2) to the lower fairing (5).
Remove the cap. Set the parts aside for re-installation. Remove the screw (7), rubber washer (8) and locknut (10) and the clamp (9) that attaches the bottom of the lower fairing to the engine guard and set aside. Remove the two locknuts (3), U-bolt (6) and U-bolt retainer (4). Remove the lower fairing by sliding it out from behind the engine guard. Repeat Steps 1 through 4 for the opposite side. Proceed to For All Models section.
For Model FLTR/I (Road Glide) with Harley-Davidson Genuine Motor Accessory Lower Fairings Disconnect negative (-) battery cable first. If positive (+) cable should contact ground with negative (-) cable connected, the resulting sparks can cause a battery explosion, which could result in death or serious injury. Disconnect the battery, negative (-) battery cable first, following the instructions in the appropriate Service Manual.
Remove the seat following the instructions in the appropriate Service Manual. Remove the cable strap holding the clutch cable to the engine guard. See Figure 2. Remove the TORX screw (8), rubber washer (9) and locknut (11) and the clamp (10) that attaches the bottom of the lower fairing (4) to the engine guard and set aside INSTALLATION 1. Hold the engine guard in position, and loosely fasten the top of the guard with the new hex socket screw and flat washer from the kit. Install the bottom brackets to the motorcycle frame with the two new TORX screws and locknuts.
Tighten all three screws to 15-20 ft-lbs (20.3-27.1 Nm). For Model FLHTCUI (Ultra Classic Electra Glide) with Factory-Installed Lower Fairings 1. Install the lower fairings following the instructions in the appropriate Service Manual. For Models FLHR/I (Road King), FLHT (Electra Glide Standard) or FLHTC/I (Electra Glide Classic) with Harley- Davidson Genuine Motor Accessory Lower Fairings 1. Carefully place one lower fairing in position from behind the engine guard. See Figure 1.
Install the lower fairing to the top of the new engine guard with the U-bolt (6) from the back, through the holes at the top of the fairing. Install the retainer (4) in position on the U-bolt and secure to the engine guard with the two locknuts (3).
Do not tighten the locknuts at this time. Attach the bottom of the fairing to the engine guard with the clamp (9) removed earlier. Install the clamp around the engine guard in the direction shown, with the tabs toward the rear of the vehicle and the flat side of the clamp against the lower fairing.
Insert the screw (7) through the lower fairing, rubber washer (8) and clamp (9). Secure the assembly with the locknut (10).
Tighten to 12 ft-lbs (16.3 Nm). Incoming search terms:. Fit the stand using the M8x18 screw to fasten it and the spring provided (photo 1 6). We suggest you to remove the stand during competitions as it could be dangerous and bruising. 18- Fit the gear lever lhoto 171.
19- Fill the fuel tank (See section 4.13). 20- Check the engine oil level (See section 4.3). INTRODUCTION Always ensure that the motorcycle has been efficiently serviced and check it over before riding it. Take your motorcycle to an authorised POIJNI MOTOR1 dealer for all maior servicing and repair.
Because of the manufacturer’s policy OF continuous development, and because of constant innovations in technology, your motorcycle may differ in some details from that described in the illustrations and text in this manual. Original POLlNl MOTOR1 spare parts are always made from the same materials and in the same way as the parts originally fitted to your minicross motorcycle. Always insist on original POIJNI MOTOR1 spore parts. Their use ensures a longer life and improved efficiency for your motorcycle. STARTING THE ENGINE FOR THE FIRST TIME Always check over your motorcycle thoroughly before starting the engine.
To start the engine for the first time, as instructed below. 1 – Turn the fuel tap located under the fuel tank to #ON” position (photo 18) Run your new motorcycle in as instructed How to ensure that the engine and transmission bed in correctly and to ensure continuous reliability in Future. The first time yw ride your new motorcycle, ride for about two hours at low engine speeds to ensure that it runs in correctly. Also respect the following precautions. 2- Once the engine starts, leave it idle until it warms up to normal temperature.
If you switch the engine off for a short time, wait for it to cool down completely before you re-start it. – 3- During the running in period, always ride at constant 2- Before starting the engine put the gear in neutral position speeds. AVOID RAPID ACCELERATION.
(photo 19, gear N). 4- Even when riding at low engine speeds, avoid extended A WARNING! IF the gear position is not neutral the bike could move when started. 3- If the engine is cold, lift the choke lever on the carburettor (photo 20). Lower the starter lever again as won as the engine starts to warm up.
4- Leove the throttle closed. Pivot the kick-start lever out wards and push energetically downwards with your foot to start the engine. 5- Return the kick-start lever to its rest position. Leave the engine idle for a few minutes to warm it up.
Check that the engine stop button stops the engine effectively before yw begin riding the motorcycle. Difficult sections of road or Lck that could cause the engine to become very hot. 5- Once you have run in your motorcycle following all these instructions, take it to a Polini Motori dealer for its post- running-in service. Apart from a change of spark plug and engine oil, this service also includes the disassembly Incoming search terms:. Instrument panel (fig.
4) 1) LCD (see page13). 2) Tachometer (rpm).
Indicates engine revs per minute. 3) Neutral (N) indicator ( green ). Illuminates when the gearbox is in neutral. 4) Fuel warning light ( yellow ). Illuminates when there are approximately 3litres of fuel left in the tank. 5) Turn signal indicator light ( green ).
Illuminates and flashes when the turn signal is in operation. 6) Engine oil pressure warning light ( red ). Illuminates when engine oil pressure is too low. This light should illuminate when the ignition is switched to ON and should go out a few seconds after the engine starts.
Important If this light (6) stays on, stop the engine to avoid serious damage. 7) High beam warning light ( blue ). Illuminates when the high beam headlight is on. 8) “EOBD engine diagnostics light” ( amber ). The engine ECU iluminates this light steadily to indicate the presence of errors leading to engine lock. 9) OVER REV indicator lights.
Illuminates steadily at 800 rpm before intervention of the revlimiter. Starts flashing when the rev limiter is reached. 5 8 2 4 9 3 1 6 7 fig. 4 12 E 10) 2-position switch A and B. Switch used for displaying and setting instrument panel parameters.
It has two positions, A “▲” and B “▼”. 11) High beam headlight flasher switch (fig. The high beam headlight flasher switch is also used for the LAP and USB data aquisition functions. 11 A 10 B fig. 5 13 E LCD – Main functions Warning Any adjustments to the instrument panel must only be carried out when the motorcycle is stationary. Never operate the instrument panel controls while riding the motorcycle.
1) Speedometer. Indicates road speed. Shows total distance travelled. 3) Trip meter. Indicates the distance travelled since last reset.
4) Fuel reserve trip counter. Shows distance travelled on reserve fuel.
6) Air temperature indicator. 8) Rev counter (RPM). 8 11 13 12 14 10 4 5 9 6 2 3 1 7 fig. 6 14 E 10) Service indicator (fig. The indicator illuminates to signal when a service is due.
The service indiactor will remain on the display until the system is reset by the Ducati Service Centre who carry outthe service. 11) LAP function (fig. Indicates that the LAP has been activated. 12) DDA function (fig. Indicates that the Ducati Data Analyzer (DDA) has been activated. Important The instrument panel incorporates diagnostic functions for the electronic injection/ignition system. The relative menus are for the use of trained personnel only.
If you accidentally access this function, turn the key to OFF and have the motorcycle checked at an authorised Ducati Service Centre. 13) Oil temperature indicator (fig. Important Stop riding if the temperature reaches the maximum value, otherwise the engine might be damaged.
14) Ducati Traction Control (DTC) (fig. Indicates activation of the DTC control unit (if present). 15 E LCD – How to set/display parameters At key-on (key turned from OFF to ON ) the instrument panelactivates all the digits of the LCD for 1second and switches on the indicator lights in sequence. Installation To prevent accidental vehicle start-up, which could cause death or serious injury, remove maxi-fuse before proceeding.
(00251a) 1 WARNING 1 WARNING ® Kit Numbers 41279-04, 41282-04, 41463-05, 41467-05, 41633-05, 41634-05, 41640-05, and 41639-05 1 of 3 Figure 1. Rear Wheel Removal i02495 1. Axle (keep) 2. Axle adjuster (keep) 3. Axle nut (keep) 4. “E”-clip (keep) 5.
Spacer (3) (keep) 6. Torx screw (5) (replace) 7. Brake disc (keep) 8. Wheel assembly (replace) 9. Valve cap (keep) 10. Compensator bowl (keep) 11.
Compensator cushion (keep) 12.12 pt screw (5) (keep) 13. Lockwasher (5) (keep) 14. Sprocket assembly (keep) 1. Refer to the Service Manual and follow the MAXI-FUSE instructions to remove the right-side cover and maxi- fuse.
Proceed to Step 2 for the wheel being replaced. Rear Wheel 2. See Figure 1. Remove the rear wheel per the REAR WHEEL, REMOVAL instructions in the Service Manual. Disassemble, clean and inspect all parts to be re-used per Service Manual instructions. Re-assemble all saved components to the new chrome rear wheel assembly.
See REAR WHEEL, ASSEMBLY in the Service Manual. Do not re-use brake disc screws. Re-using disc screws can result in torque loss and damage to rotor and/or brake assembly. Fasten the brake disc to the valve stem side of the wheel using the Torx®screws from the kit. Install the compensator bowl with the 12-point screws and lockwashers saved earlier. Install the new wheel to the rear fork. Refer to REAR WHEEL, INSTALLATION in the Service Manual.
Car Owners Manual
Proceed to Step 7. Front Wheel 2. See Figure 2. Remove the front wheel per the FRONT WHEEL, REMOVAL instructions in the Service Manual.
Disassemble, clean and inspect all parts to be re-used per Service Manual instructions. Mark the left and right brake discs so they can be re-installed to the same location. Re-assemble all saved components to the new chrome front wheel assembly. See FRONT WHEEL, ASSEMBLY in the Service Manual.
Do not re-use brake disc screws. Re-using disc screws can result in torque loss and damage to rotor and/or brake assembly.
Using the Torx ® shoulder bolts from the kit, and the saved spring washers fasten the brake discs to the same side of the wheel from which they were removed. Install the new wheel to the front forks per the FRONT WHEEL, INSTALLATION instructions in the Service Manual. Proceed to Step 7. Front and Rear Wheels 7. Refer to the Service Manual and follow the MAXI-FUSE instructions to replace the maxi-fuse and right-side cover. After servicing brakes and before moving motorcycle, pump brakes to build brake system pressure. Insufficient pressure can adversely affect brake performance, which could result in death or serious injury.
(00279a) After servicing the brake system, test brakes at low speed. If brakes are not operating properly, testing at high speeds can cause loss of control, which could result in death or serious injury. (00289a) Maintenance and Cleaning Chrome parts must be maintained regularly to ensure that they keep their original shine and luster. Clean heavily-soiled wheel surfaces using Harley Wheel and Tire Cleaner, part number 94658-98, applied with Harley Wheel and Spoke Brush, part number 43078-99. Thoroughly clean chrome with a good quality chrome cleaner, such as Harley Bright Chrome Cleaner, part number 94683-99. After cleaning and polishing, seal the finish with a good quality sealer such as Harley Glaze Polish and Sealant, part number 99701-84 Incoming search terms:. Remove existing front wheel assembly.
Save axle, axle nut, brake disc, and wheel spacers for kit installation. Refer to FRONT WHEEL in service manual.
For FLSTC and FLSTN Models: Discard moon-style hub cap.J04065 1 of 8 For FXSTD Models: Discard the tapered r ight side wheel spacer. Do not re-use brake disc/rotor screws. Re-using these screws can result in torque loss and damage to brake components.
(00319c) NOTE. For Kits 43573-08, 43575-08, 43703-08, 43978-07, 43771- 07, 43609-07, 44323-07, 44282-07, 44322-07, 43975-07, 43602-07 and 43773-07 install short valve stem (43157- 83A) included in the installation kit. For Kits 40943-09, 40966-09 and 40996-09 install long valve stem (43206-01) included in the installation kit.
See Figure 2. Install valve stem assembly (L, M or N) on wheel. Refer to TIRES in service manual. Assemble wheel installation kit components and brake disc(s) to wheel, using the appropriate service parts table. Refer to FRONT WHEEL in Service Manual. NOTES Install the primary bearing first using appropriate service manual and WHEEL BEARING REMOVER/INSTALLER. For Kits 43573-08, 43575-08, 43703-08, 43978-07, 43771-07, 43609-07, 40943-09, 40966-09 and 40996-09:.
The left side of the wheel has a machined groove (item 5, Figure 2) in the hub face and/or DOT markings to identify it as the brake disc and primary bearing side. Install the wheel so that the valve stem is on the right side of the motorcycle. For Kits 44323-07, 44322-07 and 44282-07:.
Install the wheel so that the hub markings are on the left side of the motorcycle. The left side of the wheel has a machined groove (item 5, Figure 2) in the hub face and hub markings to identify it as the primary bearing side. These kits include one or two hub plates (43985-00) to install between the brake disc and the wheel and a chrome hub cap (43986-00) to install on the wheel opposite the brake disc side. Hub covers must be installed to prevent water intrusion, which could cause an imbalance condition. Dual brake disc models: Install one stainless steel hub plate (3) between each brake disc and wheel hub. Discard chrome hub cap (2).
Install brake discs according to service manual procedures. Single brake disc models: Install one stainless steel hub plate (3) between the brake disc and wheel hub. Install the brake disc according to service manual procedures.
Install the chrome hub cap (2) on the side opposite the brake disc. Discard extra stainless steel hub plate (3). The gross axle weight ratings is unaffected by the installation of this wheel on a vehicle equipped with a 21-inch wheel. For Kits 43975-07, 43773-07, and 43602-07:. The wheel has a machined groove (item 5, Figure 2) in the hub face to identify the right side. For 2007 and later FX Softail Models and 2008 and later FXDWG: The left side of the wheel is the primary bearing side. For all other models the right side of the wheel is the primary bearing side.
For Kit 43602-07: An arrow is engraved into the right side hub to indicate the direction of rotation. For Kits 43975-07 and 43773-07: An arrow is cast between the spokes on the right side to indicate the direction of rotation. These kits include one or two hub plates (43985-00) to install between the brake disc and the wheel and a chrome hub cap (43986-00) to install on the wheel opposite the brake-disc side. Hub covers must be installed to prevent water intrusion, which could cause an imbalance condition. Dual brake disc models: Install one stainless steel hub plate (3) between each brake disc and wheel hub. Discard chrome hub cap (2). Install brake discs according to service manual procedures.
Single brake disc models: Install one stainless steel hub plate (3) between the brake disc and wheel hub. Install the brake disc according to service manual procedures. Install the chrome hub cap (2) on the side opposite the brake disc. Discard extra stainless steel hub plate (3). Install wheel assembly parts from the appropriate Service Parts table for this fitment and stock brake disc.
Discard parts from the installation kit that are not required. Refer to FRONT WHEEL in Service Manual. For FLSTC and FLSTN Models: Install wheel kit and right side wheel spacer provided in installation kit. For FXSTD Models: Install wheel kit, stock left wheel spacer and right side wheel spacer from installation kit in place of the tapered right side wheel spacer discarded in Step 1. Refer to FRONT WHEEL in service manual.
For FXSTS Models: Install the left side wheel spacer provided in the kit between the stock left wheel spacer and the left fork. All other models: Install wheel spacers previously removed. Install front wheel (1), stock axle and stock axle nut.
Refer to FRONT WHEEL in service manual Incoming search terms:. Chassis number The chassis number is stamped on the right side of the steering head tube. Enter this number in the field on page no 1. Engine number, engine type The engine number and the engine type are stamped into the left side of the engine below the engine sprocket. Enter this number on page 1. Clutch lever The clutch lever 1 is located on the left side of the handlebars.
The adjusting screw A is used to change the original position of the clutch lever (see maintenance work on chassis and engine). The clutch is hydraulically actuated and adjusts itself automatically. Hand brake lever The hand brake lever 2 is mounted on the handlebars on the right and actuates the front wheel brake. The adjusting screw B can be used to change the basic position of the hand brake lever (see maintenance work on chassis and engine). OPERATION INSTRUMENTS » 1 2 A B ENGLISH 6 OPERATION INSTRUMENTS » TEST All of the display segments briefly light up for the display function test. WS (wheel size) The display changes and the circumference of the front wheel is briefly displayed in millimeters (2205 mm corresponds to a front wheel circumference of 21″ with production tires).
Afterwards the display will return to the previous display mode. Electronic speedometer The display in the electronic speedometer is activated as soon as you press a button on the speedometer or an impulse is received from the wheel sensor. The display lights up when the engine is running. The display is cleared if no button is pressed for 1 minute or no impulse is received from the wheel sensor. The button is used to change between display modes. The + and – buttons are used to control various functions. SPEED display mode / H (service hours) Only the SPEED / H and SPEED / ODO display modes are activated in the condition at delivery.
SPEED/H is displayed whenever the display is activated and the front wheel is not turning. It automatically changes to the SPEED/ODO display mode as soon as the front wheel starts turning. SPEED displays the speed.
H displays the engine’s service hours. The service hour counter starts to count as soon as you start the engine. The displayed figure cannot be changed. Service intervals are indicated in service hours for some KTM offroad motorcycles, making the service hour counter a very practical function. SPEED / ODO display mode (odometer) The SPEED/ODO mode displays the speed and the total distance traveled. The display automatically changes to the SPEED/H display mode when the front wheel stops turning. + button no function – button no function briefly press buttonchanges to the next display mode hold button 3 secs.
Changes to the next display mode The electronic speedometer has a number of display modes (functions) that you can also activate (reveal) (see: Activating and deactivating display modes). ENGLISH 7 OPERATION INSTRUMENTS » SPEED / LAP (lap time) display mode You can use the manual stop watch to stop and store up to 10 lap times, which you can view in the LAP/LAP display mode (see below). LAP displays the lap times in hours, minutes and seconds. + button Starts and stops the stop watch, lap time is not reset to 0 – button Stops the stop watch, stores the lap time and restarts the stop watch again. The time is reset to 0. A total of 10 lap times can be stored.
If the lap time continues to run after you press the – button, all 10 memory locations are occupied.To clear all of the stored lap times, hold the button for 3 seconds in the SPEED/LAP mode.Up to 10 lap times can be stored in this way. Briefly press buttonChanges to the next display mode.If no lap time is stored or the motorcycle is driving, the LAP/LAP mode will be skipped. Hold button 3 secs. Clears all LAP figures SPEED / CLK (time) display mode CLK displays the time in hours, minutes and seconds.
+ button no function – button no function briefly press buttonchanges to the next display mode hold button 3 secs. Set the clock menu To set the clock, see „Setting the clock”. Activating and deactivating display modes In the display mode SPEED/H, press and hold the button for 3 seconds to access the SETUP menu.
The active functions will be displayed. The blinking function can be activated by pressing the + button and deactivated by pressing the – button.
Press and hold the button 3 seconds to store the settings. If no button is pressed for 20 seconds, the setting will be stored automatically and the display will return to the SPEED/H mode. + button activates the blinking display – button deactivates the blinking display briefly press buttonchanges to the next display without changing any settings hold button 3 secs. Starts the SETUP stores the settings and changes to the SPEED/H mode Incoming search terms:. Repair manual KTM 250 / 300 / 380 Art No 3206004 -E 2-2C main jet jet needle jet needle air control screw idle adjusting screw idle jet throttle valve Idling range A Operation with closed throttle valve. This range is influenced by the position of the air control screw 1 and the idle adjusting screw 2. Only make adjustments when the engine is hot.
To this end, slightly increase the idling speed of the engine by means of the idle adjusting screw. Turning it clockwise produces a higher idling speed and turning the screw counterclockwise produces a lower idling speed. Create a round and stable engine speed using the air control screw (basic position of the air control screw = open by 1.5 turns). Then adjust to the normal idling speed by means of the idle adjusting screw. Opening up B Engine behavior when the throttle opens. The idle jet and the shape of the throttle valve influences this range. If, despite good idling-speed and part-throttle setting, the engine sputters and smokes when the throttle is fully opened and develops its full power not smoothly but suddenly at high engine speeds, the mixture to the carburetor will be too rich, the fuel level too high or the float needle is leaking.
Part-throttle range C Operation with partly open throttle valve. This range is only influenced by the jet needle (shape and position). The optimum part-throttle setting is controlled by the idling setting in the lower range and by the main jet in the upper range. If the engine runs on a four-stroke cycle or with reduced power when it is accelerated with the throttle partly open, the jet needle must be lowered by one notch. If then the engine pings, especially when accelerating under full power at maximum engine revs, the jet needle should be raised. If these faults should occur at the lower end of the part throttle range at a four-stroke running, make the idling range leaner; if the engine pings, adjust the idling range richer. Full throttle range D Operation with the throttle fully open (flat out).
This range is influenced by the main jet and the jet needle. If the porcelain of the new spark plug is found to have a very bright or white coating or if the engine rings, after a short distance of riding flat out, a larger main jet is required. If the porcelain is dark brown or black with soot the main jet must be replaced by a smaller one.
Mixture too rich: too much fuel in proportion to air mixture too lean: not enough fuel in proportion to air 1 2 OPERATING RANGES OF THE CARBURETOR 2-3C Carburetor adjustment Basic information on the original carburetor setting The original carburetor setting was adapted for an altitude of approx. 500 meters (1600 ft.) above sea level, and the ambient temperature of approx. 20°C (68°F), mainly for off-road use and central European premium-grade fuel (ROZ 95 MOZ). Mixing ratio 2-stroke motor oil: super fuel 1:40 – 1:60. Basic information on a change of the carburetor setting Always start out from the original carburetor setting. Essential requirements are a clean air filter system, air-tight exhaust system and an intact carburetor.
Experience has shown that adjusting the main jet, the idling jet and the jet needle is sufficient and that changes of other parts of the carburetor will not greatly affect engine performance. RULE OF THUMB: Incoming search terms:.